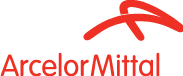
12
Financial processes automated
Standardized
Entire close process
Built-in
Auditing and governance
Company overview
ArcelorMittal, the world’s leading steel and mining company, has 168,000 employees, a presence in 60 countries and steelmaking facilities in 17 countries. Its annual crude steel production totals 71.5 million metric tons, with iron ore production reaching 58 million metric tons. The company’s goal is to be the steel company of the future by helping build a better world with smarter, stronger, cleaner, reusable steels.
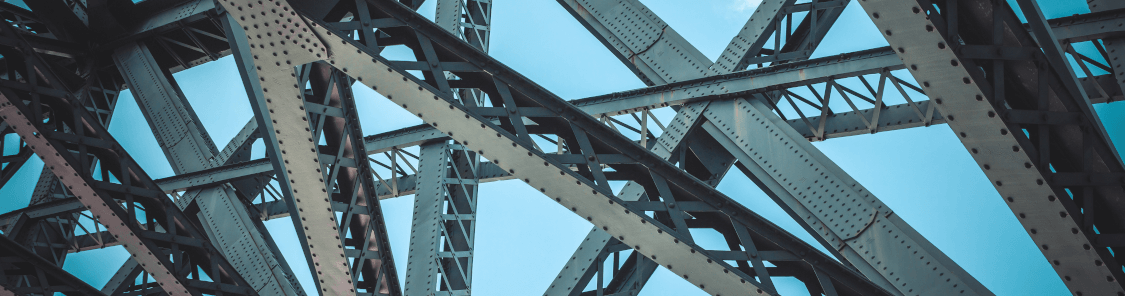
Business challenges
In the highly commoditized and competitive steel market, ArcelorMittal knew that price was its only significant differentiator. To achieve an edge over its competitors, the company had to drive efficiencies and cost savings across every single aspect of its production and processes.
By centralizing offshore activities in six Shared Services Centers (SSCs), ArcelorMittal had maxed out process efficiencies by standardizing close activities. There was a limit to the potential cost savings due to the commitment to manual processes by the remaining six SSCs.
While consolidating into a single, central SSC would have boosted efficiency and reduced costs, ArcelorMittal had no choice but to identify alternative solutions that would be acceptable to the labor unions.
Solution
ArcelorMittal selected Finance Automation by Redwood because of the platform’s focus on optimization, automation and financial control.
Results
Automation strategically targeted optimization to help ArcelorMittal maximize its financial control and significantly reduced costs to better differentiate itself in a highly competitive marketplace. The team standardized processes and realized a range of efficiencies across the global business.
Finance Automation’s built-in audit and governance capabilities offer the transparency and traceability required by ArcelorMittal’s various stakeholders.
The company relied on Redwood’s solution to automate preparation steps and eliminate reconciliations as well as manual activities related to record-to-report (R2R) and other financial processes.
Processes automated for ArcelorMittal include:
- Audit reporting
- Automated SAP closing transactions
- Closing calendar
- Doubtful debt provision
- DSO and cash planning
- GR/IR
- Intercompany
- Journal entry management
- Payment approval and processing
- Rule-based controls
- Stock-in-transit reporting
- Sub-ledger and other reconciliations
The platform automated the company’s inconsistent business processes and replaced them with standardized actions that are repeated for every single close. As expected, this greatly improves the quality of the data and accelerates each close. In addition to the cost and time efficiencies, the automation also freed up shared services finance and accounting teams to focus on value-added activities that make better use of their skills and expertise.